Production process of aerated concrete
September 14, 2021
1. Material preparation procedure
The raw materials used for the production of aerated concrete are first transported into the plant by various vehicles and stored in the warehouse or stock yard, and then the siliceous materials such as sand and fly ash are ground. According to the requirements of raw materials and process characteristics, they can be ground into powder and then mixed into slurry by adding water, or directly input into the ball mill to add water for wet grinding and pulping, and can also be mixed with part of lime Phosphogypsum, etc. The dragged lime is crushed, ground by ball mill and stored in powder lime bin; The cement is directly dragged by the cement tanker and then pumped into the cement silo; Aluminum powder shall be purchased regularly every month as planned and stored in a cool and dry warehouse. The reserve of raw materials is mainly to ensure the continuity of production and the stability of raw materials, and realize the reasonable proportion of raw materials from different sources and different quality, so as to meet the process requirements and produce qualified products.
The material preparation process is the preparation process of the later batching process, which makes the raw materials into materials that meet the process requirements. It not only provides convenience and possibility for batching and pouring, but also enables various raw and auxiliary materials to give full play to their physical and chemical functions. It is also the first process link that directly affects whether the whole production process can be carried out smoothly and whether the product quality can meet the requirements.
For the production of aerated concrete slabs, it is necessary to add: reinforcement processing and reinforcement mesh assembly process. Reinforcement processing is a special process for the production of aerated concrete plates, including derusting, straightening, cutting, welding, coating preparation, coating impregnation and drying. The assembly process of reinforcement mesh is to assemble the anti-corrosion reinforcement mesh into the mold according to the size, specification and relative position required by the process, and fix it so as to facilitate the formation of pouring and slurry gas generation.
2. Batching process
Batching is to measure various raw materials that have been prepared and stored for use according to certain requirements, temporarily store them in various supporting containers, and then add materials to the mixing equipment in turn according to the sequence of production process requirements for pouring operation. Batching process is a key link in the production process of aerated concrete. It is related to the rationality of batching, and has a direct and important impact on the gassing process, hardening process and the final performance of products.
3. Pouring process
The pouring process is to put the materials temporarily stored in the previous batching process into the pouring truck according to the process sequence, mix them with the pouring machine, make the mixed slurry that meets the time, temperature and consistency requirements specified in the production process, then pour it into the mold, and then form the green body through the static stop maintenance process. After various materials are put into the pouring truck, they will be fully mixed through the pouring mixer, and a series of preliminary chemical reactions will occur. Pouring process is an important process whether aerated concrete can form good pore structure. It constitutes the core link of aerated concrete production process together with batching process
4. Static maintenance procedure
The static curing process is mainly to promote the mixture slurry after pouring to continue to complete the gas expansion and thickening, and finally complete the growth and high hardening of the green body in the mold, so as to make the aerated concrete green body reach a certain cutting strength and facilitate cutting processing. The hardening of aerated concrete body mainly depends on the materials with hydration ability inside the aerated concrete body and the heat released by the chemical reaction, but the external ambient temperature can not be ignored. Generally, there is not much operation in the static maintenance process. Most manufacturers attach great importance to the impact of ambient temperature and are equipped with ambient temperature regulation facilities.
5. Cutting process
The cutting process is to segment and process the appearance of aerated concrete embryo to meet the requirements of appearance size of aerated concrete products. The cutting process reflects the characteristics of large-scale mechanized production of aerated concrete. By using a special cutting machine, the appearance dimensions of aerated concrete products can be flexible and diverse, so as to meet the needs of users. The working condition of cutting machine not only directly determines the appearance quality and some internal quality of aerated concrete products, but also directly affects the production efficiency of the whole aerated block production line. Therefore, in the production process of aerated products, we must pay close attention to the cutting process.
6. Autoclave curing process
Autoclave curing process is a process of high-pressure steam curing of aerated concrete blank. The production of autoclaved aerated concrete must undergo sufficient time under saturated steam curing at appropriate temperature and pressure, so that the green body can complete a series of physical and chemical changes, so as to produce due strength and become the qualified product we need. The suitable temperature for autoclave curing is above 175 ℃. Under such high temperature, high humidity and closed environmental conditions, the interior of aerated concrete blank will undergo sufficient hydration reaction to generate required tobermorite hydrate and other hydrates to form the required compressive strength. Steam curing operation should be standardized and appropriate, otherwise some problems will occur. In serious cases, there will be more waste products, which will affect the yield of products.
7. Outlet process
Autoclave discharging process is the last process of aerated concrete production, including autoclave discharging, hoisting, breaking, inspection and packaging of aerated concrete products. The out of kettle process is the guarantee for us to provide qualified products to the market and the normal operation of the next production cycle.
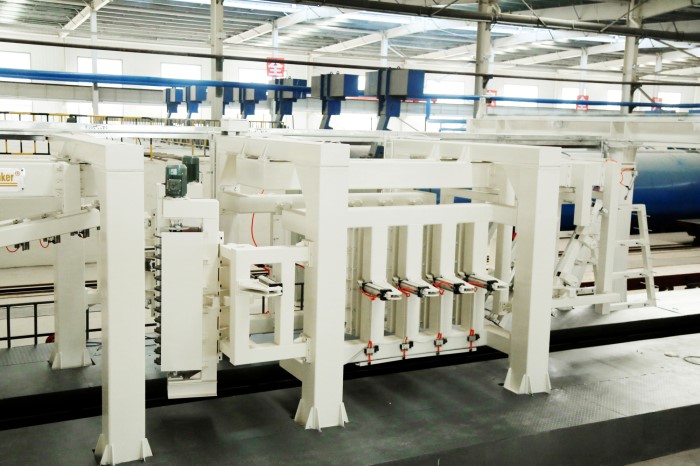